Just about anyone who solders frequently these days has heard a bit about this new product called Wire Glue. It is purported to be an inexpensive version of silvered epoxy or other conductive adhesives that utilize epoxy resin type technologies combined with various types and amounts of precious metals and other conductive materials.
Wire Glue sounds fantastic. It is very inexpensive at a few dollars for a small .3oz jar. It is advertised as being a replacement for soldering, and to those of us who do not know how to solder properly or (like me) are very rusty at it and just dislike the whole process, this sounded terrific. Well.. The best way I can describe how well Wire Glue works is to say, keep practicing your soldering. Get really good at it. It actually is not that difficult. The problem most people have (like me currently) is not having the right equipment.
Wire Glue definitely has its advantages to be sure. I think everyone should have some on hand because I will list a few uses where this stuff would indeed be great. Generally speaking though, this product is never going to replace soldering in its current form.
I tried using it on one of my attempts at making a homemade atomizer/cartomizer crossover mutant. This is a design I have been working on for a couple of months now, and so far I have nothing good to report, but that is because of my soldering skills being sooooo rusty and I have had crap irons, crap tips and no flux. Ever try working with nichrome wire without flux, it is not fun. If ever you wanted clean flat solder connections, this is the time.
I thought wire glue would be excellent because it does not require heat, and you do not have to worry about melting anything or globbing up your solder. Well, I would be better off with solder by far on this project. So let me tell you the truth about Wire Glue. Too many people are either tooting the horns of Wire Glue (salesmen and manufacturers) or completely vilifying it as evil incarnate. It actually lies somewhere in the middle of all that.
What is good about Wire Glue
* You do not need any heat to apply wire glue, so no melted insulation, components, pcb, etc
* It can be used to repair broken tracings on a PCB easily
* It can be used to add VERY TINY amounts of resistance to a connection
* It can be used on heat sensitive surface mount components
* It uses microcarbon (bucky balls) technology which is really cool stuff
* It is easy to clean off
* It is lead free
* It is safer than soldering
What is bad about Wire Glue
* It has NO stickiness and goes on as THIN as water wanting to run everywhere
* It takes several long minutes of holding parts/wires together before drying enough to let go
* It takes 8-12 hours before being completely dry and bonded
* It adds resistance to a connection (albeit in VERY TINY amounts)
* I can not find the precise resistance spec's for this stuff
* I can not find current tolerances for thi stuff
* It dries to a consistency of charcoal and needs to be coated with superglue or epoxy to make it a truly strong bond
So it has pluses and minuses. It is not a complete failure like some claim though. It definitely has uses and I will be using it, but I will not be putting away my soldering iron by any stretch of the imagination. I do suggest buying some. Go to Amazon or Think Geek and you will find it.
If you want something that does what Wire Glue is supposed to do, which is act like solder, be sticky like glue and dry to a solid bond, then look around for conductive epoxy. These will basically be actual resin type glues that contain particles of silver, gold or even platinum. They are very expensive, but if you have lots of money to throw around and hate soldering, go for it.
I would give a review of these Conductive epoxy types, but I can not afford to buy them to try them, so you are on your own with those.
Feel free to use this thread to show us any uses you have found for Wire Glue. I am very interested in successes using this product, because so many people who are not profiting from it just outright decry this stuff as a completely useless waste of money. I disagree and think it is not what thay make it sound like, but it has its uses and is not as bad as all that.
The worst part is that it is like water and difficult to apply properly. It doesn't take THAT long to dry but it seems like a long time when you are holding parts together, and because it is not sticky at all, the pieces are really easy to move if you are using your hands like me. I still have not gotten myself some helping hands/mini-vices. Once you have some applied and dry enough to let go, then I would recommend applying a second coat to assure good conductive connection, before putting on superglue or epoxy.
So you know.. The manufacturer actually recommends coating with superglue to strengthen the bond, so that should tell you something right there.
Hope this helps someone!
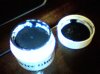
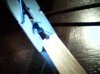
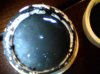
Mark Linehan
Wire Glue sounds fantastic. It is very inexpensive at a few dollars for a small .3oz jar. It is advertised as being a replacement for soldering, and to those of us who do not know how to solder properly or (like me) are very rusty at it and just dislike the whole process, this sounded terrific. Well.. The best way I can describe how well Wire Glue works is to say, keep practicing your soldering. Get really good at it. It actually is not that difficult. The problem most people have (like me currently) is not having the right equipment.
Wire Glue definitely has its advantages to be sure. I think everyone should have some on hand because I will list a few uses where this stuff would indeed be great. Generally speaking though, this product is never going to replace soldering in its current form.
I tried using it on one of my attempts at making a homemade atomizer/cartomizer crossover mutant. This is a design I have been working on for a couple of months now, and so far I have nothing good to report, but that is because of my soldering skills being sooooo rusty and I have had crap irons, crap tips and no flux. Ever try working with nichrome wire without flux, it is not fun. If ever you wanted clean flat solder connections, this is the time.
I thought wire glue would be excellent because it does not require heat, and you do not have to worry about melting anything or globbing up your solder. Well, I would be better off with solder by far on this project. So let me tell you the truth about Wire Glue. Too many people are either tooting the horns of Wire Glue (salesmen and manufacturers) or completely vilifying it as evil incarnate. It actually lies somewhere in the middle of all that.
What is good about Wire Glue
* You do not need any heat to apply wire glue, so no melted insulation, components, pcb, etc
* It can be used to repair broken tracings on a PCB easily
* It can be used to add VERY TINY amounts of resistance to a connection
* It can be used on heat sensitive surface mount components
* It uses microcarbon (bucky balls) technology which is really cool stuff
* It is easy to clean off
* It is lead free
* It is safer than soldering
What is bad about Wire Glue
* It has NO stickiness and goes on as THIN as water wanting to run everywhere
* It takes several long minutes of holding parts/wires together before drying enough to let go
* It takes 8-12 hours before being completely dry and bonded
* It adds resistance to a connection (albeit in VERY TINY amounts)
* I can not find the precise resistance spec's for this stuff
* I can not find current tolerances for thi stuff
* It dries to a consistency of charcoal and needs to be coated with superglue or epoxy to make it a truly strong bond
So it has pluses and minuses. It is not a complete failure like some claim though. It definitely has uses and I will be using it, but I will not be putting away my soldering iron by any stretch of the imagination. I do suggest buying some. Go to Amazon or Think Geek and you will find it.
If you want something that does what Wire Glue is supposed to do, which is act like solder, be sticky like glue and dry to a solid bond, then look around for conductive epoxy. These will basically be actual resin type glues that contain particles of silver, gold or even platinum. They are very expensive, but if you have lots of money to throw around and hate soldering, go for it.
I would give a review of these Conductive epoxy types, but I can not afford to buy them to try them, so you are on your own with those.
Feel free to use this thread to show us any uses you have found for Wire Glue. I am very interested in successes using this product, because so many people who are not profiting from it just outright decry this stuff as a completely useless waste of money. I disagree and think it is not what thay make it sound like, but it has its uses and is not as bad as all that.
The worst part is that it is like water and difficult to apply properly. It doesn't take THAT long to dry but it seems like a long time when you are holding parts together, and because it is not sticky at all, the pieces are really easy to move if you are using your hands like me. I still have not gotten myself some helping hands/mini-vices. Once you have some applied and dry enough to let go, then I would recommend applying a second coat to assure good conductive connection, before putting on superglue or epoxy.
So you know.. The manufacturer actually recommends coating with superglue to strengthen the bond, so that should tell you something right there.
Hope this helps someone!
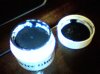
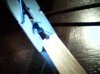
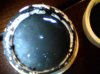
Mark Linehan
