Let me start by saying that this is simply how I build my Micro-Gen atomizers. It's based on the tools and supplies that are available to me. Please feel free to improvise as you see fit or as your own tools & supplies dictate.
Just a heads up, I do use some small power tools, including a hand drill, a small drill press, a Dremel tool and soldering iron. You can hurt yourself using any one of these items, so please, only attempt to follow these directions if you are comfortable using these types of tools. If you do decide to attempt to follow these directions, you are doing so at your own risk. I will not assume any responsibility for any type of injury that results from you following any part of these directions!
Q... What the hell is a Micro-Gen?
A... It's a really small genisis style dripping atomizer. It's about the size of a normal cartomizer.
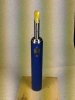
I first described it in the thread... http://www.e-cigarette-forum.com/forum/atomizer-mods/377820-micro-genesis-dripping-rba.html
Since then, a few people have asked me how it's made... So here goes...
Here are the supplies you'll need to make the atomizer itself... (You'll also need your choice of wick and wire)

Additional tools and supplies will be listed with the steps in which they are first used. This will allow you see how it's being used and determine for yourself weather of not you want to use the same items as me
The unit consists of 3 sections:
1) The base section & negative post
2) The positive post.
3) the body.
I'll start with the base section...
1) Disassemble the 808 to 510 adapter...

2) Fire up your soldering iron. You'll want to be sure to use a lead free, food safe solder.
I use a solder comprised of 96% tin & 4% silver (96SN-4AG), with a rosin core.
DO NOT USE SOLDER THAT CONTAINS LEAD!
3) You'll notice that the base of the adapter has two holes. You'll want to cover them both...
One can be covered with the IC Pin, the other with a blob of solder.
Just a heads up, I do use some small power tools, including a hand drill, a small drill press, a Dremel tool and soldering iron. You can hurt yourself using any one of these items, so please, only attempt to follow these directions if you are comfortable using these types of tools. If you do decide to attempt to follow these directions, you are doing so at your own risk. I will not assume any responsibility for any type of injury that results from you following any part of these directions!
Q... What the hell is a Micro-Gen?
A... It's a really small genisis style dripping atomizer. It's about the size of a normal cartomizer.
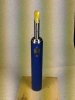
I first described it in the thread... http://www.e-cigarette-forum.com/forum/atomizer-mods/377820-micro-genesis-dripping-rba.html
Since then, a few people have asked me how it's made... So here goes...
Here are the supplies you'll need to make the atomizer itself... (You'll also need your choice of wick and wire)

Additional tools and supplies will be listed with the steps in which they are first used. This will allow you see how it's being used and determine for yourself weather of not you want to use the same items as me
The unit consists of 3 sections:
1) The base section & negative post
2) The positive post.
3) the body.
I'll start with the base section...
1) Disassemble the 808 to 510 adapter...

2) Fire up your soldering iron. You'll want to be sure to use a lead free, food safe solder.
I use a solder comprised of 96% tin & 4% silver (96SN-4AG), with a rosin core.
DO NOT USE SOLDER THAT CONTAINS LEAD!
3) You'll notice that the base of the adapter has two holes. You'll want to cover them both...
One can be covered with the IC Pin, the other with a blob of solder.
Last edited: